Monitoring and management of the EHDS is implemented at specialized places - an automated operator's workstation (AWS) and control cabinet screens (CC), which can be placed both on the thermal control panel and “in situ” next to the turbine unit in the turbine shop. The workstations and screens contain the following information:
- video frames of alarms and protections;
- necessary controls for setpoints and mode switches;
- indicators of the value of regulator setpoints, the position of servomotors, and controlled quantities;
- window for visualizing graphs of EHDS parameters in real time and in retrospective mode.
- normalized primary control of the turbine rotor speed with insensitivity no more than ±10 MHz;
- power regulation according to the proportional-integral law with an accuracy of no worse than ±0.5 MW;
- regulation of steam pressure in production extraction;
- regulation of steam pressure in district heating extraction;
- regulation of temperature or heating of network water;
- effective frequency correction of the power regulator when the network frequency deviates beyond the programmable settings;
- formation of mode switchings;
- manual control mode;
- effective limitation of a number of parameters:
- restrictive regulation of the minimum fresh steam pressure (by unloading the turbine);
- restrictive regulation of maximum steam pressure in production extraction;
- restrictive regulation of the maximum steam pressure in the chamber of the control stage of the high-pressure cylinder;
- restrictive regulation of maximum steam pressure in district heating extraction;
- effective limitation of rotation speed in case of sudden complete or incomplete (with preservation of own needs) load shedding with or without disconnecting the generator from the network;
- maintaining tests to check the tightness of stop and control valves;
- automation of the process of turning and loading the turbine unit:
- initialization of hydraulic protection according to signals from the automated process control system, or at the command of the driver;
- passing critical zones at a given pace when turning;
- automatic change of speed controller tempo in synchronization mode.
- anti-acceleration control functions;
- anti-overclocking protection functions implemented both in the turbine controller and using an independent 3-channel speed control system and protection against overspeed for each half-set of ECSR. The described configuration fully complies with the requirements of GOST R IEC 61508 (IEC 61508) for the SIL3 safety integrity level.
- shock-free transition under load from one adjustable parameter to another upon command from the automated process control system, or upon command from the driver;
- automatic, shock-free transition from one regulator to another if technologically necessary;
- generating a signal to turn off the turbine due to an unacceptable increase in the angular acceleration of the turbine rotor and transmitting it to the control circuit for the turbine shutdown electromagnets;
- emergency control based on emergency automatic control commands;
- testing of anti-overclocking protection channels with the turbine stopped, at idle and under load without increasing the rotation speed;
- automatic transition to manual circuit control mode in the event of failure of the sensor of the controlled parameter - “survival strategy”;
- automatic transition of the EGSR to an autonomous mode of operation in the event of a failure of communication with the automated process control system of the turbine unit;
- continuous self-diagnosis of the electronic part with signaling of detected failures and deviations of the ACS parameters.
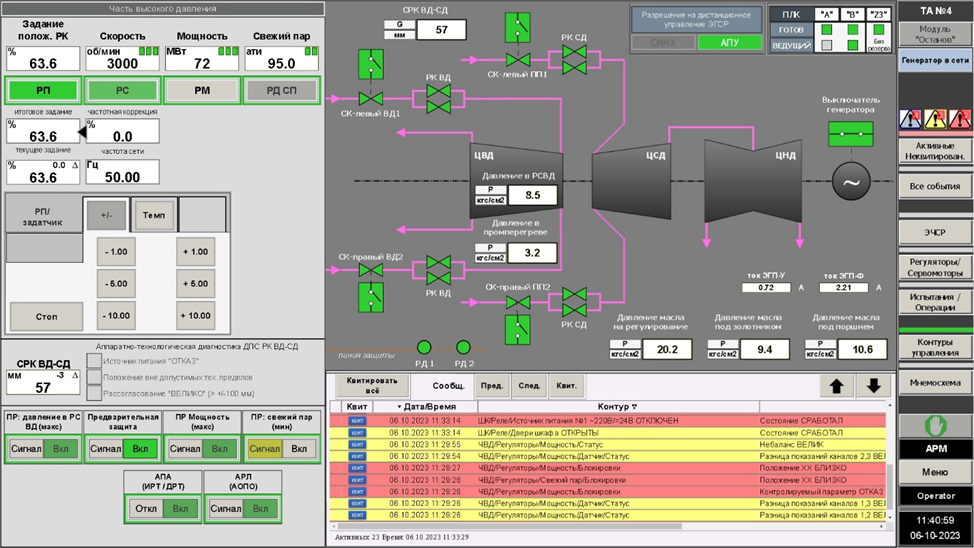
Drawing. An example of a form from the AWS screen (turbine unit K-210-130 when operating in a network under load)
The automated workplace provides the ability to control the turbine:
- in test mode;
- in start and stop mode;
- in normal operating modes of a turbine installation with automatic or manual control of the turbine’s electrical load;
- with technological limitations;
- in emergency modes of the turbine unit and power system;
- in post-emergency modes of the power system.
Also in standard EGSR projects, the following solutions and functionality, which have become almost standard, are implemented:
- duplication and tripling of responsible elements of the EGSR;
- speed control using a proportional-integral regulator at idle speed, simplifying synchronization with the network;
- use of analysis of the dynamics of increasing rotor speed to effectively limit the rotation speed during load shedding;
- special algorithms that ensure interaction of control loops (the so-called “mutual assistance of regulators”);
- providing anti-overclocking protection functions with support for checking channels without accelerating the turbine;
- proportional-integral power control with feedback on the active power of the generator and frequency correction to ensure primary frequency control;
- regulation of steam pressure in extractions with a given degree of unevenness;
- additional limiting pressure regulators in regulated steam extractions, duplicating the functions of hydraulic extraction protection systems;
- protection when the generator enters asynchronous mode;
- software and hardware solutions providing a “survival strategy” for the system.
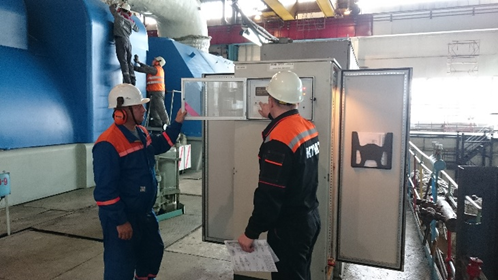
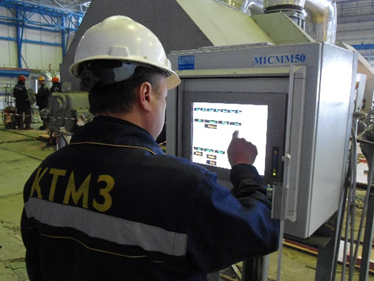